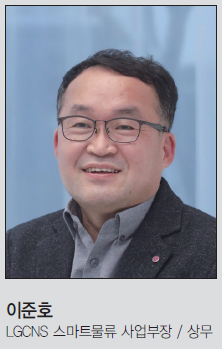
3. 자동화 설비의 운영 최적화
오토스토어를 도입한 자동화 설비 기반의 MFC를 살펴보자. 오토스토어는 [그림 6]과 같이 로봇(Robot), 빈(Bin), 그리드(Grid), 포트(Port)로 구성되어 있다. 출고 지시를 내리면 최상단에 로봇이 해당 주문의 상품이 보관된 빈을 찾아 설비와 작업자 간 접점인 포트(입고 또는 출고 작업장)로 이송한다. 작업자는 주문에 해당하는 상품을 빈에서 피킹하는 자동화 설비이다.
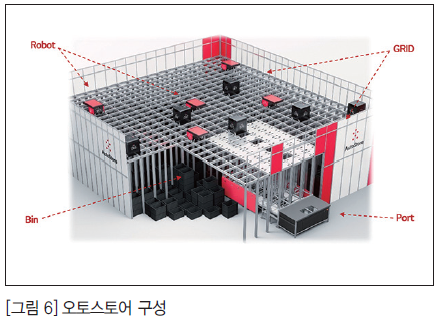
이처럼 상품이 작업자에게 다가오는 피킹 방식을 GTP(Goods To Person) 방식이라고 한다. 오토스토어는 작업(Task) 단위의 그룹화 방법(Task Group)에 따라 2가지 방식으로 출고 지시가 가능하다. 첫 번째는 주문 단위의 출고 지시 방식이다. 예를 들어 2개의 주문이 있다고 가정하면 1번 오더에 해당하는 상품이 담긴 모든 빈이 출고되고, 그 이후에 2번 오더와 관련된 모든 빈이 출고된다. 주문 단위로 처리하는 개별 오더피킹 방식과 유사하다.
두 번째는 총량 피킹(배치피킹) 방식의 출고 지시이다. 총량 피킹 방식은 주문에 해당하는 상품을 담은 모든 빈이 반출되지만 주문 단위로 반출되지 않아 상품을 주문 별로 완성하기 위한 분류 작업이 추가로 필요하다. 분류 작업은 빈 상자 1개가 고객 주문과 1:1로 매핑되어 있다. 이처럼 총량 피킹한 상품을 분류 작업장에서 상품 스캔을 통해 고객별, 지역별로 분류하는 피킹 시스템을 “Pick-and-Sort” 방식이라고 한다. 일반적으로 대규모의 주문 처리를 위해 자동화 설비를 도입한 MFC는 차량의 배차 시간을 고려하여 일정 시간 동안 접수된 주문을 모아서 차수(Shift) 단위로 작업 지시를 내린다.
오토스토어의 운영에서 주문 처리를 위해 반출되는 빈의 수를 줄이면 작업 시간의 단축이 가능하다. 최적화의 듀얼 이론(Duality Theory) 관점에서 반출되는 빈의 수를 최소화하는 문제는 반출하는 빈에서 피킹 수를 증가시키는 문제와 동일하다.
국내 업계에서는 반출되는 Bin 당 평균 피킹 수를 배치 피킹률(Batch Factor)라고 부른다. 배치 피킹률의 산식은 “Σ오더라인 수/Σ빈 반출 수” 또는 “Σ반출 상품의 수량/Σ빈 반출 수”이다. 배치 피킹률이 2.5이면 빈 1회 반출에 상품 2.5개를 꺼낸다. 2.5개의 오더 라인을 대응한다는 의미로 수치가 높을수록 효율적이다. 빈 반출에 대한 효율화는 재고 할당과 밀접한 관계가 있다. [그림 7]과 같이 재고 할당 방법에 따라 반출 빈의 수가 달라지는 것을 볼 수 있다. 이는 자동화 설비를 어떻게 운영하는지에 따라 성능이 달라질 수 있다는 것을 의미한다.
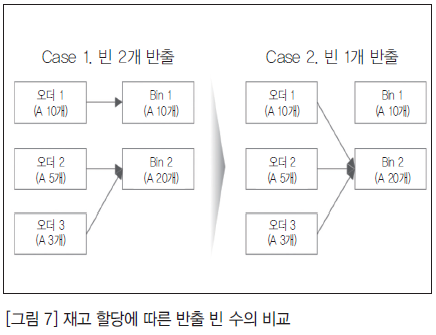
오토스토어의 도입 및 운영을 위해서는 배치 피킹률의 분석과 재고 할당에 대한 알고리즘은 필수이다. LGCNS는 오토스토어의 보관 SKU, SKU별 재고 일수, Bin의 규모, 주문 데이터 분석을 통해 배치 피킹률을 분석하는 시뮬레이터와 빈 반출을 최소화하기 위한 재고 할당 알고리즘을 개발하였다.
최근 주문량의 증가와 운영 효율화 관점에서 고비용의 자동화 설비를 도입하는 유통기업이 증가하고 있다. 자동화 설비 도입이 목표 처리량을 보증하지는 않는다. 도입한 설비를 어떻게 운영하는지에 따라 목표 처리량을 초과 달성할 수 있고, 처리량이 기대에 미치지 못할 수 있다. LGCNS는 “Pick-and-Sort” 방식을 운영 중인 유통기업을 대상으로 배치크기, 총량 피킹 작업, 토트의 분류 작업장 할당 등 운영 방식을 분석 및 개선하여 처리량을 10~20%를 증가시킨 경험이 있다.
운영 방식의 개선을 위해서는 프로세스 및 데이터 분석을 통해 비효율이 발생하는 원인과 인과관계를 도출해야 한다. 그리고 해결해야 하는 문제를 목적, 제약사항, 결정 변수로 구조화하고 문제 해결을 위한 적합한 방법론을 찾아야 한다. 해법으로는 물류설비의 도입, 레이아웃의 개선, 프로세스의 개선, 최적화 및 인공지능 기법을 적용하는 로직 개선 등이 있다.
주의해야 할 점은 프로세스에서 한 부분만 효율화하는 것이 아닌 주문이행 시간의 단축, 인건비의 절감 등 시스템 전체 관점에서 어떤 개선 효과가 있는지 살펴봐야 한다. 프로세스에서 병목 공정이 아닌 다른 공정의 개선 작업은 처리량에 대한 개선 효과가 없는 것과 일맥상통한다.
코로나19 이후 구매패턴의 변화 등으로 인해 물류센터에서 합포의 난이도와 복잡도가 더욱 증가하고 있다. 프로세스 개선을 위한 방향성의 설정, 적절한 해법의 선택 등에 대해서는 물류 전문기업에 컨설팅을 의뢰하는 것이 좋다.
지금까지 MFC의 운영 효율화 관점에서 다양한 문제를 살펴보았다. MFC 운영 기업은 앞에서 다룬 문제 이외에도 중앙물류센터(CFC, Central Fulfillment Center)와 MFC의 네트워크 전략, CFC에서 MFC로 상품 배분, 재고관리, 수요예측, 물류센터 구축, 자동화 설비 도입 등 다양한 의사결정 문제를 마주하고 있다. 전체 최적화를 위해서는 다양한 의사결정 문제를 전략/전술/운영 수준으로 분류하고 각 문제 간의 연관성을 고려해 계획을 수립하고 실행해야 한다.
LGCNS는 컨설팅부터 설계, 시뮬레이션, 센터 및 시스템 구축, 운영까지 물류센터의 모든 것을 책임지는 TLSP(Total Logistics Solution Provider)이다. [그림 8]과 같이 LG CNS는 300여 건 이상 물류센터 관련 프로젝트를 경험한 정예 전문가들이 고객 상황에 가장 적합한 물류센터 구축 서비스를 제공한다.
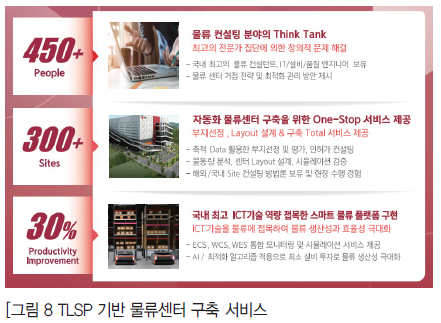