층고를 활용한 보관 밀도 상승 및 생산성 극대화
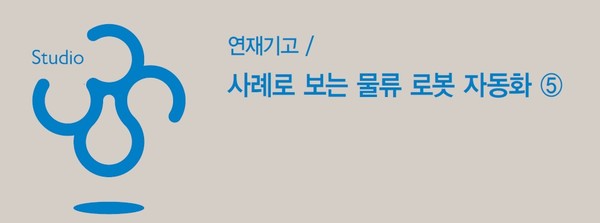
최근 코로나로 인해 지속적으로 물동량이 증가하면서 AGV로봇을 통한 자동화에 대한 관심이 높아지고 있다. 늘어나는 물동량을 신속하게 처리할 수 있는 시스템 구축이 기업 생존을 좌우하는 요인으로 작용하고 있기 때문이다. 여기에 효율적인 물류창고(센터) 운영을 통한 보관의 중요성도 덩달아 높아지고 있다. 특히 최근 물류창고(센터)의 공급보다 수요가 많아 사용할 수 있는 물류창고(센터)의 공간을 찾기 어려워지면서 기존의 공간 효율성을 높이려는 시도들이 늘어나고 있다. 이번에 소개할 사례는 스마트한 물류창고(센터) 관리로 효율을 높인 ‘유도(YUDO)’이다. 플라스틱 사출 금형에 핵심 부품인 핫러너를 생산하는 유도는 원자재 창고에 자동화 시스템을 도입해 효율적으로 운영하고자 했다.
부족한 공간과 인력 문제로 어려움 겪어
유도는 물동량 증가에 따른 보관 공간 부족현상이 가장 심각한 문제였다. 유도의 경우 박스나 파렛트를 평치에 적치해 높은 층고를 활용하지 못하고 있었다. 물동량은 지속적으로 증가하는데 보관공간의 부족으로 인해 원자재 관리도 쉽지 않았던 상황이었다. 공간의 부족과 함께 실시간 이동 데이터 관리도 되지 않았다. 작업자가 직접 물품을 찾아 피킹하는 시스템과 작업자의 숙련도에 따라 빈번하게 발생하는 휴먼 에러로 인해 데이터 관리에 어려움이 있었다. 이에따라 업무 효율은 물론 물동량을 처리하는 속도 또한 문제가 되고 있었다. 여기에 물가 상승에 따른 인건비 증가, 노동력 공급 감소 등 부가적인 문제들도 적지 않은 상황이었다.
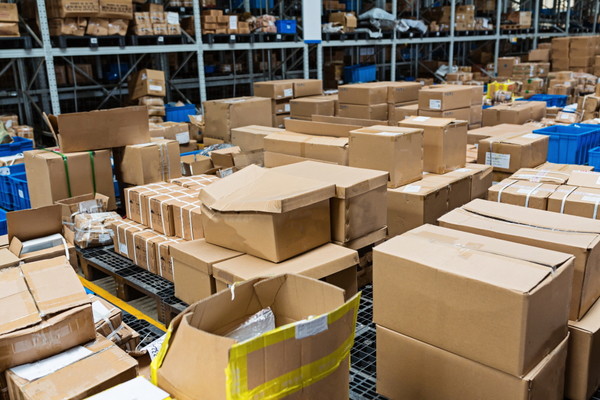
SWS 구축을 통한 효율 극대화
Studio 3S는 유도가 겪고 있는 공간과 인력에 대한 문제를 해소하기 위해 자동화 시스템 적용이 필요하다고 판단했다. 이에 SWS(Smart Warehouse System) 구축 프로젝트를 제안했다. SWS구축 프로젝트는 스마트한 창고 시스템을 구축하는 것으로 창고의 공간 효율과 보관 효율을 극대화하고, 물류를 신속하게 처리 및 관리하여 높은 회전율을 제공하는 시스템이다. 또한 다양한 크기의 상품 핸들링이 가능하며 창고 관리 시스템(WMS)과 연계로 창고 운영현황을 실시간으로 모니터링 할 수 있는 시스템이다.
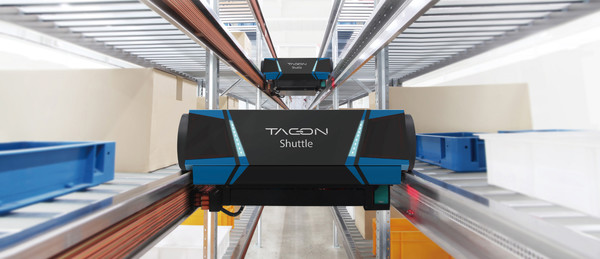
유도는 높은 층고의 물류창고(센터)를 운영하면서도 수직공간을 활용하지 않고 수평 공간만을 활용하는 평치 적치로 공간 활용의 비효율이 상당했다. 이를 해소하기 위해 높은 층고를 활용한 Rack 설치를 통해 보관 밀도를 높이고 레일을 통해 자유롭게 이동할 수 있는 TAGON Shuttle Robot 시스템을 도입하여 GTP 방식을 적용했다. TAGON Shuttle은 Rack 사이의 레일을 따라 선반 내 제품을 자동 운반하는 로봇이다. 신속하고 정확한 이송 처리로 피킹 및 적치가 가능하다. 특히, 바코드 좌표를 인식하여 스스로 위치를 포지셔닝하고 창고관리시스템인 WMS와 연계되기 때문에 물동량과 창고 회전율을 극대화할 수 있는 시스템이다.
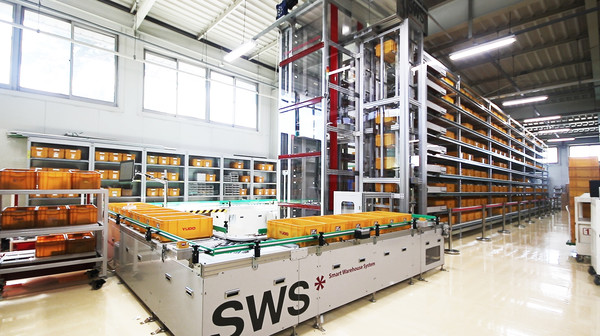
유도에 적용된 시스템은 높은 층고를 최대한 활용하기 위해 9층 높이의 Double Deep Storage를 적용, 전체 저장용량 900 Cell의 Rack과 Shuttle 3대로 구성됐다. 또한, Shuttle 전용 리프트를 이용하여 층을 이동할 수 있도록 했다. Rack을 통해 물품을 피킹 및 적치하는 입고부터 출고될 물품 박스를 피킹하고 컨베이어에 옮겨 박스를 자동으로 출고 처리 할 수 있게 구성했다. 컨베이어를 통해 입고 대기부터 주문 처리, 피킹, 출고, 그리고 다시 대기 Order 박스로 과정을 반복한다. 유도는 이 시스템을 통해 박스 간의 공간 효율을 증가시킬 수 있었다. 또한 이송 대차 AGV와 연계로 공정 간 100% 물류 자동화를 실현했으며 출고량이 증가해도 한 번에 다중 출고 처리가 가능하기에 업무효율을 개선할 수 있었다.
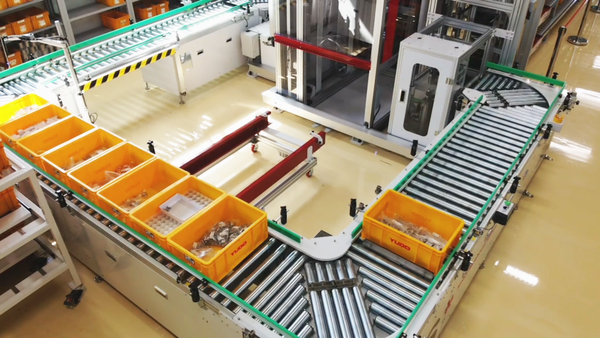
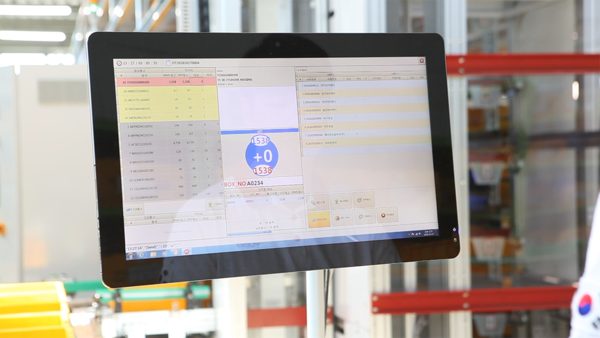
이 시스템에서 Rack과 Shuttle이 중요한 역할을 하고 있지만 이를 뒷받침 할 수 있는 S/W는 빼놓을 수 없는 중요한 요소이다. 입출고로 이동하는 물품을 실시간으로 관리하고 재고 분석은 물론, 재고데이터 추적 및 적정 재고를 파악하여 불필요한 원자재 도입을 막을 수 있었다. 또한 정확한 물류 정보를 유지, 효율적인 업무가 가능하기 때문에 업무 생산성 또한 향상됐다. 즉, 안정적이고 효율적인 물류 운영을 위한 통합 물류 관리 시스템(ILC, 원재료 및 자재의 조달에서부터 제조, 보관, 출하에 이르기까지 공장 내 이동하는 재공 및 재고에 대한 LOT 단위의 위치 이동 정보를 실시간 모니터링 하는 물류 관리 시스템), 창고 관리 시스템(WMS)을 통해 제어, 모니터링, 분석이 가능하기 때문에 S/W의 적용은 매우 중요한 포인트로 볼 수 있다.
340% 생산성 향상이라는 놀라움
유도의 수주부터 출고 완료까지의 과정을 세분화 해 확인해본 결과 전체 작업 중 가장 많은 비중을 차지하는 작업이 피킹이었다. 그동안 유도는 전체 작업 시간의 87%를 피킹 작업에 사용하고 있었다. 하지만 이번 SWS의 도입을 통해 비약적으로 피킹 작업 비중을 줄일 수 있었다. 기존의 인력을 활용하는 것과 TAGON Shuttle 시스템을 이용한 자동화 피킹을 비교해보면 기존 87% 피킹 작업 비중이 55%로 축소됐다. 이를 통해 효율적이고 높은 회전율을 제공할 수 있었다. 이는 TAGON Shuttle 특징인 빠른 스피드와 높은 처리 능력 때문이다. 또한, 전체 생산성이 3배 이상 증가하여 일일 처리 가능 용량이 증가했다. 즉, 똑같은 시간으로 더 많은 일을 처리할 수 있어 효율적인 업무 처리가 가능하게 됐다. 시간으로 계산해보면 하루 18건의 물동량을 처리하기 위해서 기존에는 2시간 51분이 소요 되었다. 건당 평균 9분 30초 정도가 소요 된 셈이다. 하지만 SWS 구축 후에는 총 50분 정도로 작업 시간을 비약적으로 줄일 수 있었다. 건당 평균 처리속도가 2분 48초로 줄어 많은 개선이 이루어졌다는 것을 알 수 있다. 이는 기존 대비 340% 생산성이 향상된 수치이다.
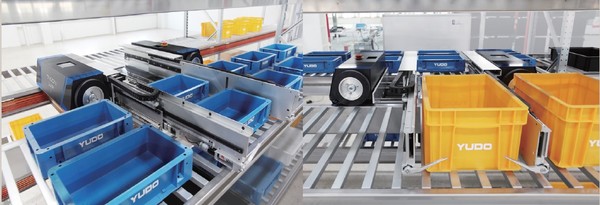
이번에 소개한 사례는 창고 자동화를 통한 공간 및 보관 효율성 극대화, 신속한 주문 처리로 높은 회전율과 생산성 향상의 효과를 본 사례로 물동량 증가로 처리 능력 및 보관 효율이 떨어져 고민인 기업자들에게 좋은 사례가 될 것이다.